Heat Recovery and Energy Reclaim in HVAC Systems
As part of our mechanical engineering services, HCE incorporates heat recovery solutions to reduce energy consumption and improve overall HVAC system efficiency. Our designs include energy reclaim from exhaust air, condenser loops, and other sources, tailored to each project’s usage profile and sustainability objectives.
Heat recovery and energy reclaim systems are essential for improving the efficiency of HVAC systems by capturing waste energy and using it to reduce the demand for primary heating or cooling. These strategies are particularly effective in buildings with significant ventilation loads, simultaneous heating and cooling requirements, or high internal heat gains. Properly designed systems can improve a building’s NABERS or Green Star performance, reduce plant size, and help meet the compliance obligations of Section J of the National Construction Code (NCC), as well as AS/NZS 1668.1, which governs mechanical ventilation and energy recovery systems.
Heat recovery is increasingly implemented in both air-side and water-side applications, often with payback periods of less than five years depending on system size, run hours, and climatic conditions. It is especially relevant in healthcare, education, laboratories, commercial kitchens, and high-performance buildings.
Air-Side Heat Recovery
Air-side heat recovery systems are used to transfer energy between the exhaust and incoming outdoor air streams, reducing the energy needed to condition ventilation air. This is particularly useful where 100% outside air is required or where exhaust air contains recoverable energy (e.g. from offices, retail, or classrooms).
Common air-side devices include:
- Rotary Heat Exchangers (Thermal Wheels): These rotating matrices can transfer both sensible and latent heat between exhaust and supply air streams. They are efficient (70–85% sensible heat recovery) but require high-quality filtration and careful maintenance to avoid cross-contamination.
- Plate Heat Exchangers (Fixed Plate or Crossflow): These static devices are used when sensible-only recovery is preferred. Efficiency typically ranges from 50–70%, and they are commonly used in hospitals and clean environments due to zero risk of cross-contamination.
- Run-Around Coil Systems: When supply and exhaust ducts are separated spatially, glycol or water coils connected by a pumped loop can transfer heat between airstreams. They offer lower recovery (40–60%) but are flexible in layout and easier to retrofit.
In all air-side recovery systems, pressure drop, frost control, condensate drainage, and air leakage must be carefully managed. Designers must also account for fan energy penalties when calculating net energy benefit. The NCC and Green Star allow energy recovery devices to contribute toward meeting minimum ventilation efficiency metrics.
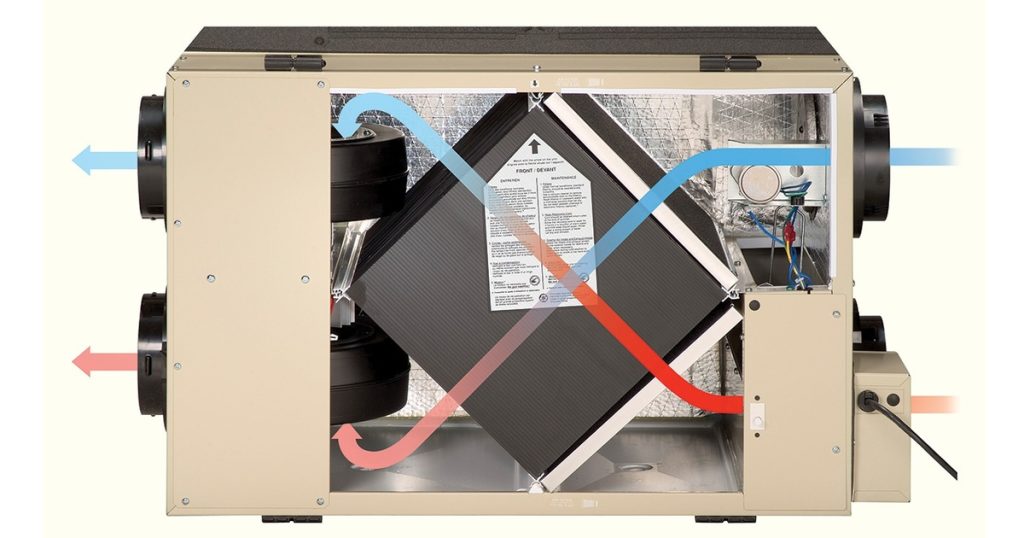
Water-Side Heat Reclaim
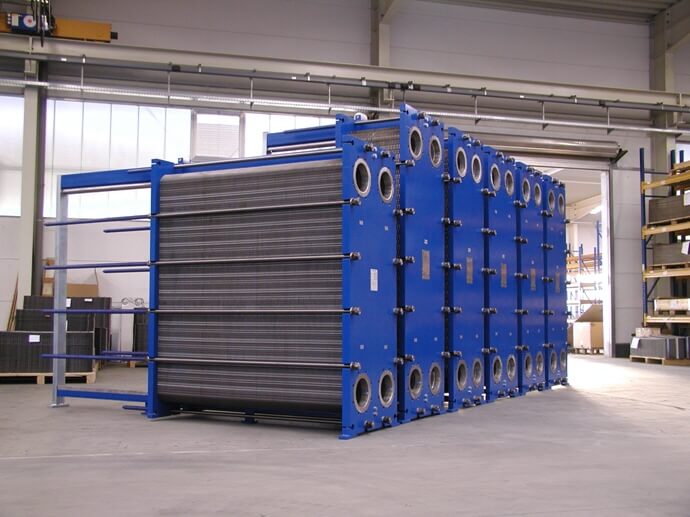
Water-side energy reclaim systems capture heat from refrigerant circuits or condenser water loops and reuse it for other thermal loads within the building, such as domestic hot water (DHW) preheating or process heating. These systems are particularly effective when simultaneous heating and cooling occurs, such as in hotels, hospitals, or mixed-mode buildings.
Key strategies include:
- Condenser Heat Recovery: Waste heat from air- or water-cooled chillers is reclaimed using a desuperheater coil or additional condenser circuit to produce warm water. Recovery temperatures typically range from 40–60°C, suitable for DHW storage.
- Heat Recovery Chillers (HRCs): These units are capable of producing chilled and hot water simultaneously, with COPs exceeding 5.0 when both circuits are fully loaded. They are especially useful in facilities with year-round cooling and heating demand, like data centres or healthcare.
- Hybrid Systems: Some VRF and hydronic systems use refrigerant-to-water heat exchangers to serve underfloor heating, reheat coils, or DHW, improving seasonal efficiency and enabling decarbonisation of gas-fired boilers.
Thermal storage tanks may be integrated to buffer heat recovery supply, decouple generation from demand, and improve control flexibility.
Applications and Control Strategies
Effective heat recovery systems must be controlled to operate only when energy reclaim is beneficial. Control logic typically includes:
- Bypass Dampers or Valves: Allowing system to disable energy recovery when conditions do not justify the pressure drop penalty (e.g. similar exhaust/supply temperatures).
- Recovery Priority Modes: For heat recovery chillers, sequencing is based on whether simultaneous load exists; otherwise, they operate in conventional cooling/heating mode.
- Temperature Differentials: Ensuring sufficient delta-T between heat source and sink to allow effective energy transfer.
- Seasonal Setpoint Adjustments: Adjusting recovery thresholds to suit varying outdoor temperatures, particularly for enthalpy wheels and economiser modes.
Performance monitoring and trending via the BMS allows building managers to validate recovery efficiency and ensure sustained operation.
Regulatory Compliance and Simulation Modelling
Both Section J5.6 of the NCC and Green Star Energy Credits reward implementation of heat recovery systems, provided minimum performance thresholds are achieved and modelled accurately. Energy reclaim systems are included in JV3 performance solutions using thermal simulation tools (e.g. IES VE, EnergyPlus), which evaluate their annual contribution to heating/cooling energy reduction.
Wherever implemented, the designer must consider:
- Structural considerations for rotary wheel or plate HX placement within AHUs.
- Hygiene and maintenance requirements under AS/NZS 3666 (particularly for run-around loops).
- Filtration and air quality where recovery occurs from contaminated zones.