Air Conditioning Systems
Air conditioning is central to our mechanical design services at HCE, where we provide detailed system selection, performance modelling, and documentation for all common system types. Whether it’s VRF, chilled water, or split systems, our designs align with client performance goals and compliance with NCC and Section J requirements.
Air conditioning systems are essential for achieving indoor environmental quality (IEQ) by maintaining optimal thermal comfort, controlling humidity, and ensuring air quality. A well-designed system not only meets occupant comfort needs but also complies with regulatory requirements such as those outlined in the National Construction Code (NCC) and relevant Australian Standards (e.g., AS 1668, AS/NZS 3666).
The appropriate air conditioning solution depends on various factors including building type, floorplate layout, occupancy patterns, energy efficiency objectives, redundancy requirements, and capital and operational cost considerations. Below, we outline the key air conditioning systems commonly deployed across residential, commercial, and institutional projects.
Variable Refrigerant Flow (VRF) Systems
Variable Refrigerant Flow (VRF) systems use inverter-driven compressors to precisely vary the amount of refrigerant delivered to multiple indoor units based on real-time cooling or heating demand. VRF systems are capable of providing simultaneous heating and cooling across different zones through the use of heat recovery technology, making them ideal for buildings with highly diverse occupancy profiles, such as hotels, office spaces, and mixed-use developments.
Piping design, including total refrigerant charge calculations and pipe branch configurations, must carefully consider manufacturer limits to ensure system efficiency and maintain compliance with refrigerant safety standards (such as AS/NZS 5149.1). VRF systems offer high part-load efficiency, individual zone control, modular expandability, and minimal spatial requirements for plant rooms compared to traditional chilled water systems.
Split Systems
Split systems are direct expansion (DX) systems comprising an indoor air-handling unit connected to an outdoor condenser via refrigerant piping. They provide heating and cooling for single zones, making them suitable for smaller projects or areas where independent climate control is preferred, such as residential dwellings, small retail units, and standalone offices.
Technical design of split systems requires accurate load calculations, careful refrigerant pipe sizing to prevent oil trapping, and adequate clearance for maintenance access and airflow performance. Modern inverter-type split systems provide variable speed control, enhancing energy efficiency under partial load conditions. However, scalability is limited, and multiple condensers may be required for larger applications, increasing façade or rooftop space demands.
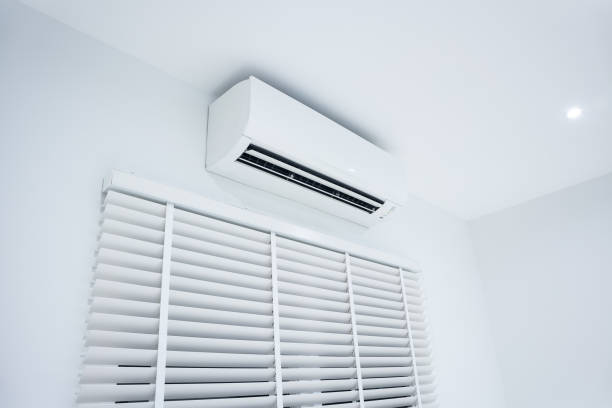
Water-Cooled Air Conditioning Systems
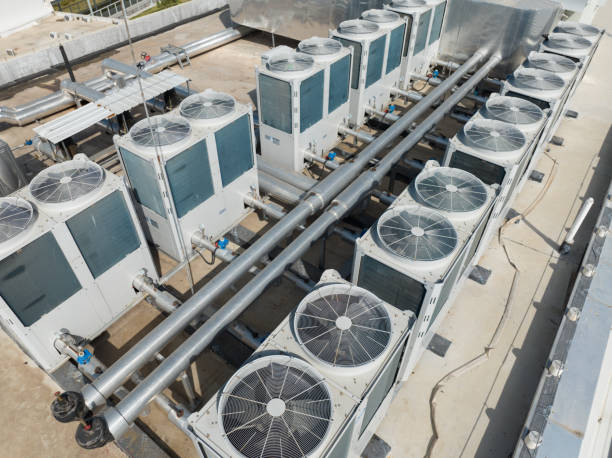
Water-cooled systems utilise water as a heat rejection medium, typically involving a closed-loop condenser water circuit connected to cooling towers. Systems such as water-cooled package units and water source heat pumps are highly efficient, particularly for high-rise and dense urban developments where air-cooled plant would be impractical due to spatial and noise constraints.
Design considerations include maintaining proper approach temperatures, minimising water treatment issues (scaling, corrosion, biological fouling), ensuring effective tower placement for prevailing wind conditions, and meeting local environmental discharge regulations. Water-cooled systems often deliver lower lifecycle costs in energy-intensive buildings due to superior thermodynamic efficiency compared to air-cooled alternatives.
Condenser Water Systems
Condenser water systems form the backbone of many large HVAC plant configurations, operating in conjunction with water-cooled chillers or modular heat pump systems. The condenser water absorbs heat rejected from the cooling cycle and transports it to cooling towers where it is expelled to the atmosphere via evaporative cooling.
System design must address key parameters such as condenser water flow rates, minimum and maximum operating temperatures (typically between 27°C to 32°C), water treatment regimes, and redundancy strategies (e.g., standby pumps and towers). Variable speed drives (VSDs) on condenser water pumps and tower fans are often employed to optimise system efficiency under varying thermal loads.
Chilled Water Systems
Chilled water systems are used to supply cooling to large-scale applications, delivering chilled water (typically at 6°C supply and 12°C return) to fan coil units (FCUs), air handling units (AHUs), and other terminal units. Central plant chilled water production is typically achieved using electric chillers (air-cooled or water-cooled), or absorption chillers powered by waste heat.
System design involves selecting between primary-only, primary-secondary, or variable primary flow (VPF) hydronic schemes, with emphasis on pump energy reduction, temperature differential optimisation (ΔT), and part-load performance. Integration with Building Management Systems (BMS) enables dynamic control of setpoints, flow rates, and staging strategies to maximise operational energy efficiency. Chilled water plants may also incorporate free cooling, thermal energy storage, or high-efficiency magnetic bearing chillers for improved performance.
Heating Hot Water (HHW) Systems
Heating Hot Water (HHW) systems are utilised for hydronic heating applications where thermal energy is needed for space heating or pre-heating ventilation air. HHW is typically produced via gas-fired boilers, electric resistance heaters, or heat pumps, and distributed at temperatures commonly ranging from 70°C to 85°C, depending on the system design and terminal units.
Design factors include pipework sizing, insulation standards (AS 4426.1), hydraulic separation techniques (e.g., low-loss headers, buffer tanks), and selection of energy sources considering efficiency, carbon footprint, and future-proofing for electrification strategies. High-efficiency condensing boilers are often employed to recover latent heat from flue gases, delivering superior seasonal performance. Water quality management through dosing and regular monitoring is essential to prevent internal corrosion and maintain heat transfer efficiency.
Packaged Air Conditioning Units
Packaged units integrate all refrigeration, air handling, and control components into a single factory-assembled unit. They are generally rooftop-mounted and supply conditioned air directly into the building via ductwork, serving large open-plan areas like supermarkets, warehouses, and big-box retail stores.
Packaged systems offer rapid deployment and reduced on-site construction risks, with pre-engineered performance characteristics. However, design flexibility is lower compared to modular or central plant solutions, and careful sizing is necessary to accommodate partial load performance. Maintenance access, outdoor sound levels, and rooftop structural loading are important considerations during project design.
Air Conditioning Systems – Technical Comparison
System Type | Typical Applications | Capital Cost | Efficiency | Scalability | Key Technical Considerations |
---|---|---|---|---|---|
VRF Systems | Offices, hotels, apartments, mixed-use | High | Very High | Excellent | Refrigerant safety compliance, zone diversity management, maintenance access |
Split Systems | Residential dwellings, retail units, small offices | Low | Moderate | Limited | Refrigerant pipe sizing, condensate management, limited simultaneous heating/cooling |
Water-Cooled Systems | High-rise towers, CBD developments | High | Very High | Excellent | Water treatment, cooling tower location, pump energy optimisation |
Condenser Water Systems | Central chilled water plants, modular heat pumps | Medium-High | High | High | Tower sizing, pipework design, variable speed controls, redundancy provision |
Chilled Water Systems | Hospitals, universities, commercial complexes | Very High | Very High | Excellent | Hydronic balancing, differential temperature management (ΔT), BMS integration |
Heating Hot Water (HHW) Systems | Hospitals, offices, aged care, educational facilities | Medium | High | Excellent | Boiler efficiency (condensing preferred), hydraulic separation, corrosion control |
Packaged Air Conditioning Units | Retail outlets, warehouses, data centres | Medium | Moderate | Limited | Structural loading, ductwork layout, site access, weatherproofing |