Humidity Control in HVAC Systems
HCE designs HVAC systems with precise humidity control for applications where indoor environmental quality is critical, such as health care, laboratories, or high-density residential. We specify appropriate system types, controls, and zoning strategies to maintain ASHRAE-recommended humidity levels year-round.
Humidity control is a critical component of HVAC design, particularly in climates with high seasonal moisture content or in buildings with strict environmental conditions such as healthcare, laboratories, museums, and data centres. Controlling humidity not only ensures occupant comfort and indoor air quality but also prevents issues such as condensation, mould growth, corrosion, and damage to building materials and sensitive equipment.
Australian guidelines, including ASHRAE Standard 62.1, ASHRAE 55, and NCC Volume 1, provide reference humidity ranges and ventilation requirements for various building types. For most comfort conditions, the target indoor relative humidity (RH) is between 40% and 60%, though tighter control may be necessary for specialised environments.
Psychrometric Principles and Moisture Loads
Humidity control begins with understanding psychrometrics — the relationship between air temperature, moisture content, and enthalpy. HVAC systems must be capable of handling both sensible heat (temperature) and latent heat (moisture). Moisture loads in a building can arise from:
- Outdoor air through ventilation or infiltration
- Occupants (perspiration and respiration)
- Equipment and processes (e.g., in commercial kitchens or gyms)
- Building materials releasing moisture (e.g., during construction drying)
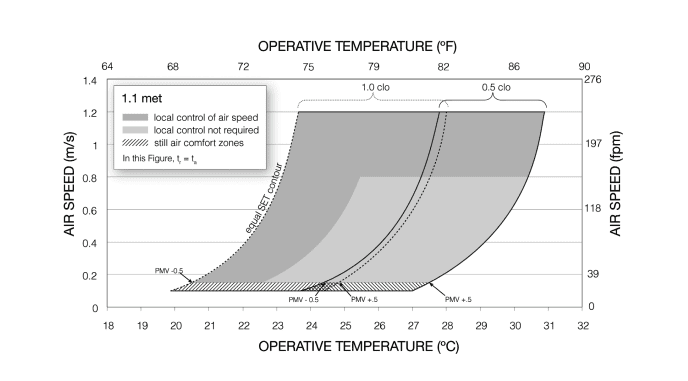
Accurate calculation of latent loads and psychrometric plotting is essential during the design stage to size cooling and dehumidification equipment correctly.
Dehumidification Techniques
here are several methods for dehumidifying air in HVAC systems. Each is selected based on the required humidity control precision, airflow rates, and energy efficiency considerations.
Cooling-Based Dehumidification
The most common method involves cooling air below its dew point using a chilled water coil or DX coil, condensing moisture on the coil surface. After moisture is removed, the air may be reheated (using reheat coils, hot gas bypass, or heat recovery) to achieve the desired supply air temperature without overcooling the space.
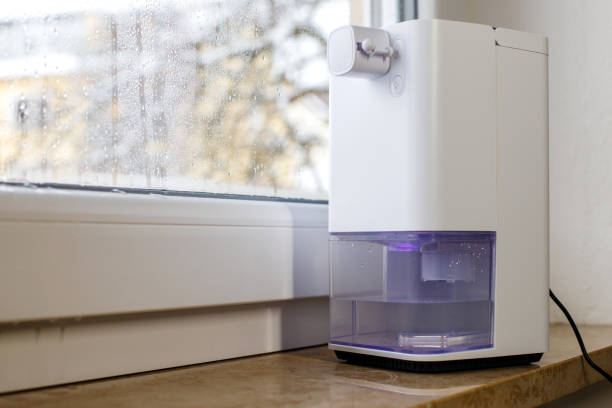
Key considerations:
- Systems must modulate coil flow or compressor output for part-load control.
- Coil surface temperature must be low enough (typically <12°C) to ensure condensation.
- Proper drainage and condensate management are essential (per AS/NZS 3666).
- Reheat is often required to avoid overcooling and improve comfort.
Desiccant Dehumidification
Desiccant-based systems use hygroscopic materials (solid or liquid) to absorb moisture. These are often used in industrial or process environments where extremely low RH is required (e.g., <35%).
- Solid desiccant wheels are regenerated using heated air, often waste heat or gas-fired sources.
- Liquid desiccant systems involve direct contact with air and are more complex but offer high capacity.
Desiccant systems can achieve dew points below 10°C, making them ideal for cold storage or pharmaceutical manufacturing. They are often used in hybrid systems paired with conventional DX or chilled water cooling.
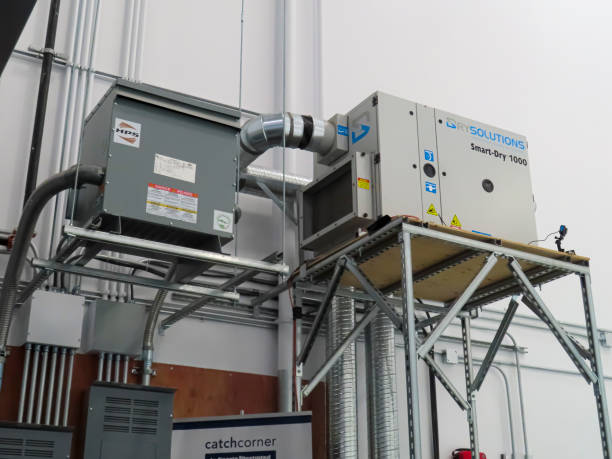
Ventilation and Moisture Control
Ventilation systems must be designed to limit uncontrolled moisture ingress. Use of enthalpy recovery wheels, run-around coils, or pre-conditioning systems helps limit the moisture load on downstream coils.
- In climates with high outdoor humidity, pre-treatment of air using overcooling and reheat becomes essential.
- Dedicated Outdoor Air Systems (DOAS) often include integrated dehumidification to treat fresh air before it reaches interior zones.
Humidification (When RH is Too Low)
While dehumidification is common in most climates, humidification may be required in colder climates or winter operation, particularly in spaces such as:
- Laboratories
- Operating theatres
- Archives/museums
- Cleanrooms
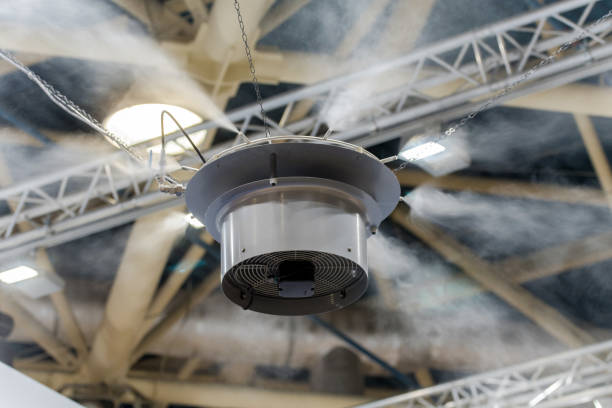
Humidification systems include:
- Ultrasonic humidifiers for precision control with minimal energy
- Steam injection (electric or gas)
- Evaporative humidifiers (adiabatic)
Each method must meet hygiene requirements under AS/NZS 3666 and be controlled to prevent condensation in ducts or rooms.
Control and Monitoring
Effective humidity control depends on precise sensing and system coordination:
- Dew point control is preferable to RH in some applications, especially in chilled beam or displacement ventilation systems where surface condensation risk exists.
- Humidity sensors (±2% RH accuracy) should be installed in both supply air and occupied zones.
- Deadband controls should prevent excessive cycling between dehumidification and humidification modes.
- BMS integration allows trending of RH values and alarms if out of range.
Design and Compliance Considerations
Designers must also address the following:
- Drainage slopes and traps for cooling coils.
- Moisture migration through walls and floors (vapour barriers, insulation).
- Thermal bridging that can lead to condensation and RH issues at structural interfaces.
- For green buildings, managing RH effectively contributes to Green Star IEQ credits and improved NABERS Indoor Environment ratings.
ASHRAE 90.1 and NCC Section J also impact the energy efficiency of systems that involve simultaneous cooling and reheating for humidity control — alternatives like energy recovery, variable dew point control, and demand-based ventilation are encouraged.