Thermal Comfort and Indoor Air Quality (IAQ)
At HCE, thermal comfort and IAQ are at the heart of every HVAC system we design. Our work considers occupant wellbeing, energy efficiency, and environmental compliance, using performance-based methods and referencing standards such as ASHRAE 55 and the NCC’s indoor air requirements.
Maintaining thermal comfort and indoor air quality (IAQ) is a fundamental objective of HVAC engineering, directly impacting occupant health, productivity, and compliance with regulatory and rating systems. A well-designed system must not only meet the architectural and operational requirements of the building but also ensure the indoor environment adheres to standards such as ASHRAE 55, ASHRAE 62.1, ISO 7730, NCC Volume 1 Section F, and AS 1668.2. Effective IAQ design requires the integration of environmental control strategies—temperature, humidity, ventilation, filtration, and contaminant management—into a cohesive mechanical system architecture. As buildings evolve toward net-zero goals, these comfort and air quality parameters must be maintained without compromising energy performance, often requiring detailed simulation and performance modelling from early design stages.
Thermal Comfort Modelling and Compliance
Thermal comfort is evaluated using models defined in ASHRAE 55 and ISO 7730, which quantify acceptable thermal environments using indices such as the Predicted Mean Vote (PMV) and Predicted Percentage of Dissatisfied (PPD). The PMV model accounts for environmental parameters (air temperature, mean radiant temperature, humidity, and air speed) and personal variables (metabolic rate and clothing insulation). Compliance is achieved when the PMV is within ±0.5 and the PPD is less than 10%. These are typically validated using dynamic thermal modelling tools such as IES VE, DesignBuilder, or EnergyPlus.
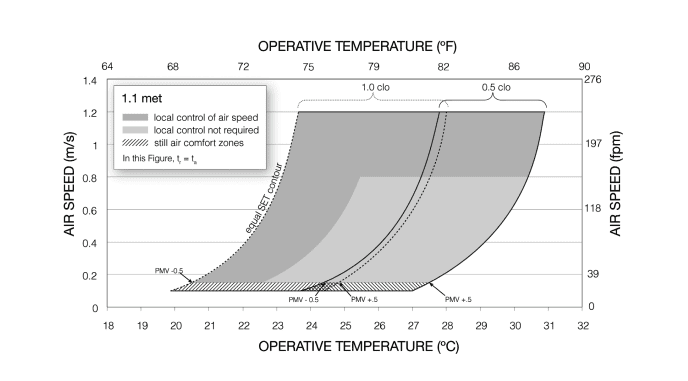
Thermal comfort zone boundaries can also be graphically represented using a psychrometric chart overlaid with comfort envelopes defined by ASHRAE 55 for various activity levels. Local thermal discomfort—caused by drafts, vertical temperature gradients, or asymmetric radiation—must also be evaluated, particularly in mechanically cooled and heated spaces. Engineers often design to maintain vertical stratification of less than 3°C between head and ankle height, with maximum air speeds under 0.2 m/s in occupied zones for sedentary activity.
Ventilation Rates and Zonal Effectiveness
Outdoor air ventilation is critical for diluting internal pollutant concentrations such as CO₂, VOCs, and particulate matter. AS 1668.2 and ASHRAE 62.1 prescribe minimum outdoor air intake rates based on zone occupancy classification, floor area, and expected pollutant loads. For example, office spaces require a minimum of 10 L/s per person, with a default occupancy density of 10 m²/person.
Designers must calculate zone air distribution effectiveness (Ez), which accounts for diffuser layout, thermal stratification, and short-circuiting. Displacement ventilation and underfloor air distribution systems may have higher Ez values (≥1.2), whereas ceiling-based systems may default to 1.0. Ventilation effectiveness (Ev) is defined as the ratio of contaminant concentration in the return air versus the breathing zone, and affects the calculation of required zone outdoor airflow (Voz).
Demand-Controlled Ventilation (DCV) systems are increasingly applied to reduce energy use in intermittently occupied spaces. CO₂ sensors are typically installed at return grilles or in representative zones, controlling modulating outside air dampers or VAV terminal airflow. For effective DCV, control algorithms must include adjustable setpoints (usually 800–1000 ppm), deadbands, and time averaging to avoid short cycling.
Air Filtration and Particulate Removal
Mechanical air filtration plays a primary role in the removal of airborne particles. Filter performance is defined by the Minimum Efficiency Reporting Value (MERV) per ASHRAE 52.2 or ISO 16890, which classifies filters by particulate size removal efficiency (PM10, PM2.5, PM1). For commercial buildings, ASHRAE recommends a minimum of MERV 13 filtration, which captures ≥85% of particles in the 1.0–3.0 μm range. Critical environments such as healthcare operating theatres or cleanrooms require HEPA (High-Efficiency Particulate Air) filters, with ≥99.97% efficiency at 0.3 μm.
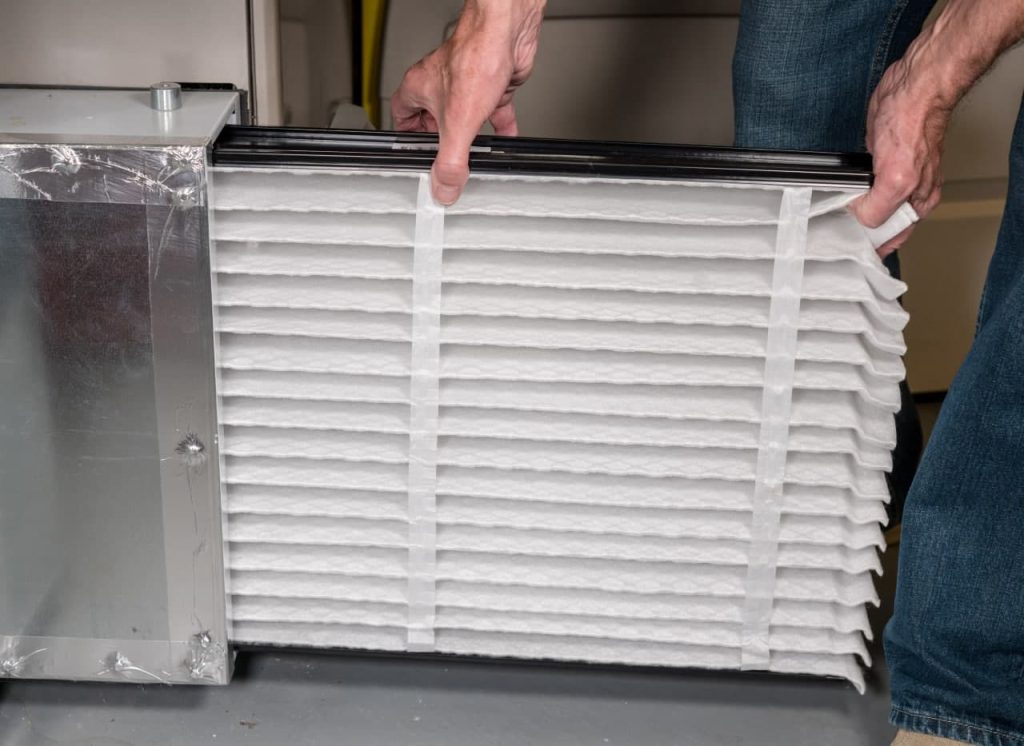
Filtration must be designed considering:
- Access panels and clearance for routine replacement.
- Pressure drop across the filter media at design airflow rates.
- Filter bypass integrity and gasket compression.
- Placement upstream of coils to prevent fouling.
In systems with variable air volume (VAV), filter loading must be considered in fan static pressure calculations to ensure consistent airflow as filter resistance increases over time. Filter monitoring systems using differential pressure switches or BACnet sensors are commonly specified for real-time status tracking.
Humidity Management and Psychrometric Control
Relative humidity (RH) affects both comfort and biological contaminant viability. ASHRAE 55 recommends an RH range of 30–60% for comfort, while ASHRAE 62.1 and the NCC require control in certain occupancy types to reduce mould risk. HVAC systems use the sensible heat ratio (SHR) to define the proportion of total cooling capacity dedicated to sensible (dry bulb) versus latent (moisture) load removal. For zones with high latent loads (e.g., gyms, pools, or healthcare), SHR < 0.70 may be required.
Dehumidification is typically achieved by cooling coils operating below dew point, often followed by reheat to restore discharge air to neutral supply conditions. Reheat can be provided via:
- Electric coils
- Hot water coils
- Hot gas bypass (in DX systems)
- Energy recovery from desiccant wheels
Active humidification is employed in facilities such as archives, laboratories, and hospitals. Humidifiers may use:
- Electric steam generation (with precise control)
- Ultrasonic units (energy efficient but water-quality sensitive)
- Direct injection of steam from a central boiler (used in large facilities)
All humidifiers must be integrated into the BMS for control, interlocked with airflow status, and located with appropriate spacing to avoid duct condensation.
Chemical and Biological Contaminant Mitigation
Advanced IAQ strategies such as photocatalytic oxidation, bipolar ionisation, and electronic air cleaners are increasingly deployed in high-occupancy and premium projects. While these technologies show promise, their effectiveness must be evaluated using independent data (e.g., UL 867, UL 2998 for ozone-free certification), and any by-products such as ozone or formaldehyde must be kept below exposure limits set by Safe Work Australia or WHO IAQ Guidelines.
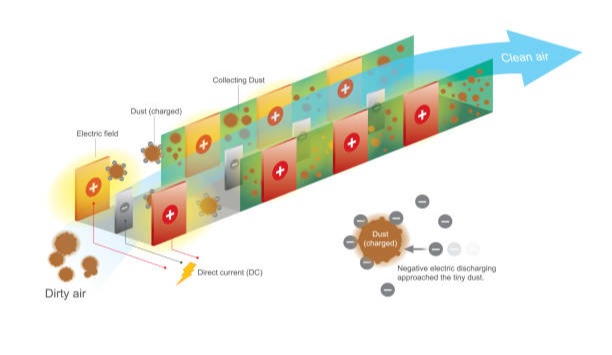
Controlling contaminants at the source is a key IAQ strategy. This includes:
- Pressurising clean zones relative to dirty ones (e.g., offices over car parks)
- Isolating equipment rooms with exhaust systems achieving 10–15 air changes/hour
- Using low-VOC paints, adhesives, and finishes during specification
- Providing local exhaust for copy rooms, kitchens, and toilets (per AS 1668.2)